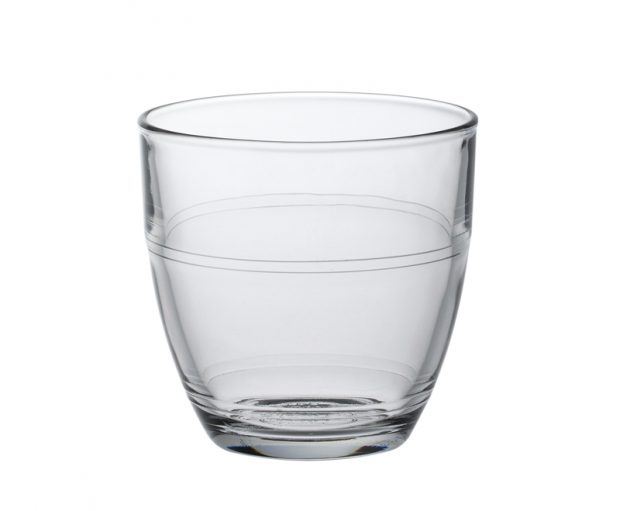
Gigogne
1946年発売のロングセラー。大きさにより6個セットで5.50~8.50€。
学校や会社の食堂、カフェやビストロ、家庭でもよく見かけるコップ(グラスというよりはコップと呼びたい)。丈夫で割れにくく底が厚いので安定感があって手になじむ。その商標が 「デュラレックス」 とは知らなくても、このコップを手にしたことのないフランス人はいないだろう。それほどフランス人の生活に浸透しているコップの工場をオルレアン郊外の工業団地に訪ねた。
デュラレックスの歴史は1930年代にガラス・建材製造サンゴバン社がオルレアン郊外ラ・シャペル・サンメスマンにあった香水瓶工場を買収したことにさかのぼる。同社はここで強化ガラス (verre trempé)を世界で初めて開発し、1945年に強化ガラスコップ、「デュラレックス」 商標を登録した。
戦後30年間の黄金時代の後、国際競争激化で90年代に業績が悪化し、デュラレックスは97年に伊企業に売却された。その後いくつかの企業を経て2008年に倒産寸前だったのを買い取ったのが、現社長のアントワーヌ・イオアニデス氏と同社幹部2人だ。
「当時私は食品業界にいたが、デュラレックスの販売に関わっていた兄弟の強い要望で経営に乗り出すことになった」と、社長は当時を振り返る。236人のうち200人の雇用を維持しつつ1年半で年商3400万ユーロ、利益340万ユーロを上げる会社に再建した(今は社員250人、年商3100万ユーロ)。
15haの広大な敷地に入ると、桂砂とソーダ灰などの原料を混ぜて炉に流し込む巨大なサイロがまず目につく。工場内に入ると、原料が1500℃の溶解炉に落ちていく様子が垣間見えた。次に、溶けてオレンジ色になったガラスの塊が円状に並んだ金型に落ちてプレスされる。
あっという間にコップの形になったものが次々に出てくる。これに冷風を噴射して急速に冷やすプロセスが trempe(焼入れ)。これで熱(130C°)や衝撃に耐える、通常のガラスより2.5倍強い強化ガラスになる。
自動車や航空機の強化ガラスを得意とするサンゴバンから受け継いだデュラレックスのノウハウだ。「製造過程はすべて自動化されているから簡単に見えるだろうが、製造する品を変えるたびに金型を替え、機械を調整しなければならない。その微調整は長年コップを作ってきた熟練工の目と感覚だけが頼り」と社長。年中不休の溶解炉は10年ごとに刷新される。今年6月末がその刷新期にあたり、8月下旬まで生産停止になる。新炉の導入で生産量を年間1億個から2倍にするのが目標だ。
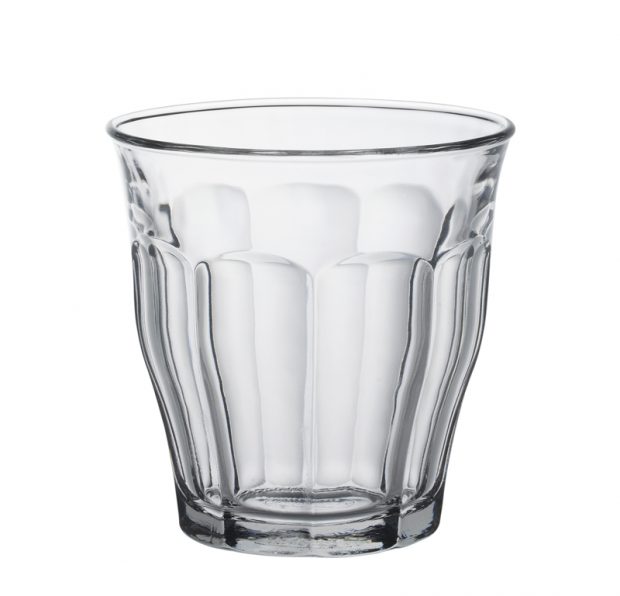
Picardie
持ちやすい指幅のくぼみの入った定番コップ。
大きさにより6個セットで5.50~10.60€
国内の販路は大型小売店ほか、地方公共団体、カフェ・レストラン、学校、病院などだが、製品の8割は世界100ヵ国(日本も)に輸出する。原料調達から最終製品まで 「メイド・イン・フランス」という付加価値が輸出の強みだ。コップだけでなくカップ、皿、タッパー、オーブン皿など商品は350種類にのぼるなか、丸型で中ほどに2本線の入ったGigogneや、持ちやすい指幅の溝の入ったPicardieなどのコップがデュラレックスの定番だろうか。シンプルさがかえってスタイリッシュで、大衆品の優れものの典型と言っていいだろう。(し)
